As an Amazon Associate, I earn from qualifying purchases
By impregnating porous materials with a resin or other sealing material, vacuum pressure impregnation (VPI) is a crucial industrial procedure that improves the performance and dependability of porous materials. This method is frequently used to stop leaks, enhance mechanical qualities, and lengthen component life in a variety of industries, including manufacturing, automotive, and electrical.
Technical Specifications
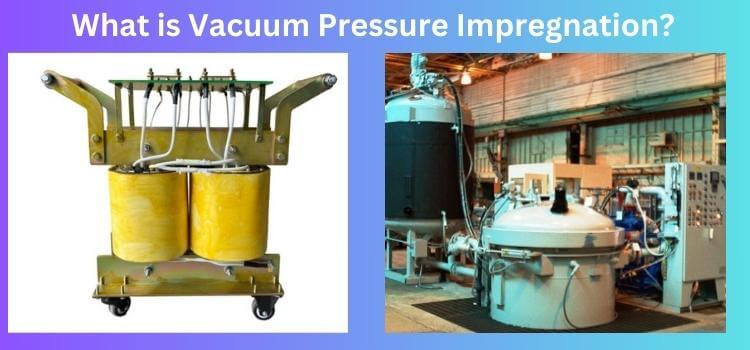
Applications
Automotive Industry
- Engine Components: Enhances the durability and leak resistance of engine blocks and cylinder heads.
- Transmission Parts: Prevents fluid leakage in transmission housings.
- Fuel Systems: Ensures the integrity of fuel injector bodies and other fuel system components.
Electrical Industry
- Motors and Transformers: Insulates and protects windings, ensuring longevity and reliability.
- Electronic Components: Seals connectors and sensors against environmental factors.
Manufacturing
- Machinery Parts: Improves wear resistance and lifespan of machinery components.
- Porous Castings: Seals micro-porosities in cast parts, preventing leakage and improving structural integrity.
Benefits
- Enhanced Sealing: Prevents leaks in porous materials.
- Improved Mechanical Properties: Increases the strength and durability of components.
- Extended Lifespan: Reduces wear and tear, leading to longer-lasting parts.
- Cost Savings: Minimizes waste and rework due to defective parts.
Challenges and Limitations
- Initial Cost: High upfront cost for VPI equipment and setup.
- Complex Process: Requires precise control of vacuum and pressure parameters.
- Material Compatibility: Not all materials are suitable for VPI, and resin selection is critical.
Latest Innovations
Advanced Resins
- High-Temperature Resins: Development of resins that can withstand higher temperatures, expanding the range of applications.
- Eco-Friendly Resins: Innovations in environmentally friendly resins that reduce environmental impact.
Automation
- Automated Systems: Integration of automation to improve the precision and efficiency of the VPI process.
Real-Time Monitoring
- Sensors and Software: Use sensors and software for real-time monitoring and control of the impregnation process.
Future Prospects
- Integration with 3D Printing: Combining VPI with additive manufacturing for enhanced part performance.
- Nanotechnology: Use of nanomaterials to improve the properties of impregnated parts.
- Sustainability: Focus on developing sustainable resins and reducing the environmental footprint of VPI processes.

Comparative Analysis
VPI vs. Traditional Sealing Methods
VPI vs. Impregnation by Immersion
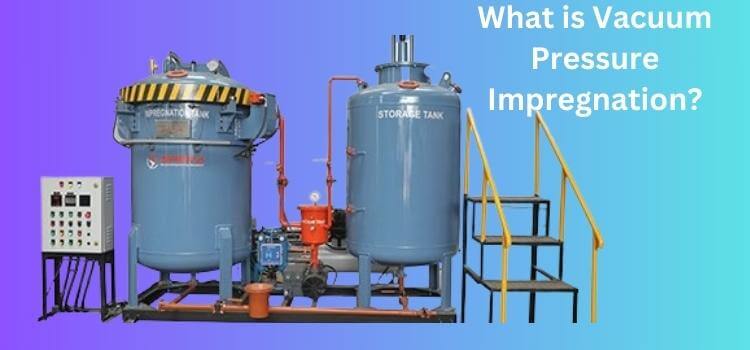
User Guides or Tutorials
Step-by-Step VPI Process
Preparation: Clean and dry the components to be impregnated.
Initial Vacuum: Place the components in the VPI chamber and apply a vacuum to remove air and moisture.
Resin Impregnation: Introduce the resin into the chamber while maintaining the vacuum.
Pressure Application: Apply pressure to ensure the resin penetrates deep into the pores.
Curing: Remove and cure the components per the resin manufacturer’s instructions.
Conclusion
Vacuum Pressure Impregnation is a transformative process that enhances the reliability and performance of porous materials across various industries. Its ability to seal micro-porosities and improve mechanical properties makes it invaluable in modern manufacturing. VPI is expected to become even more efficient and widely applicable as technology advances, ensuring the production of high-quality, durable components.
As an Amazon Associate, I earn from qualifying purchases